The life cycle of cork as a raw material begins with extraction of the cork oak bark, which is called harvesting. Cork enters the manufacturing process after it is extracted, to produce the myriad of products that we can find: stoppers, construction and design materials, among many others.
Cork Harvesting consists in the removal of the bark from cork oaks and takes place during the most active phase of cork growth, between the middle of May or beginning of June until middle or end of August.
To start harvesting a cork oak, the trunk of the cork oak has to reach a perimeter of around 70 cm when measured 1.3 meters from the ground. This takes about 25 years.
The first harvest, which is known as “desbóia”, produces cork of a very irregular structure which is too hard to be easily handled. This is the known as virgin cork which will be used for applications other than cork stoppers (flooring, insulation etc.), since its quality is far from that necessary to manufacture stoppers.
Nine years later, the second harvest produces material with a regular structure, less hard, but still not suitable for cork stoppers – this is known as secondary cork.
It is from the third and subsequent harvests that the cork with the best properties is obtained, suitable for the production of quality cork stoppers, since its structure is regular with a smooth outer and inner bark. This is what is known as “amadia” or reproduction cork. From then on, the cork oak will supply good quality cork every nine years for around two centuries, in a total, on average, of 15 bark harvests throughout its life.
The harvesting of the cork oak is an ancient process that can only (and should) be done by experts: the descortiçadores. Manual skill and a lot of experience are required to avoid damaging the tree.
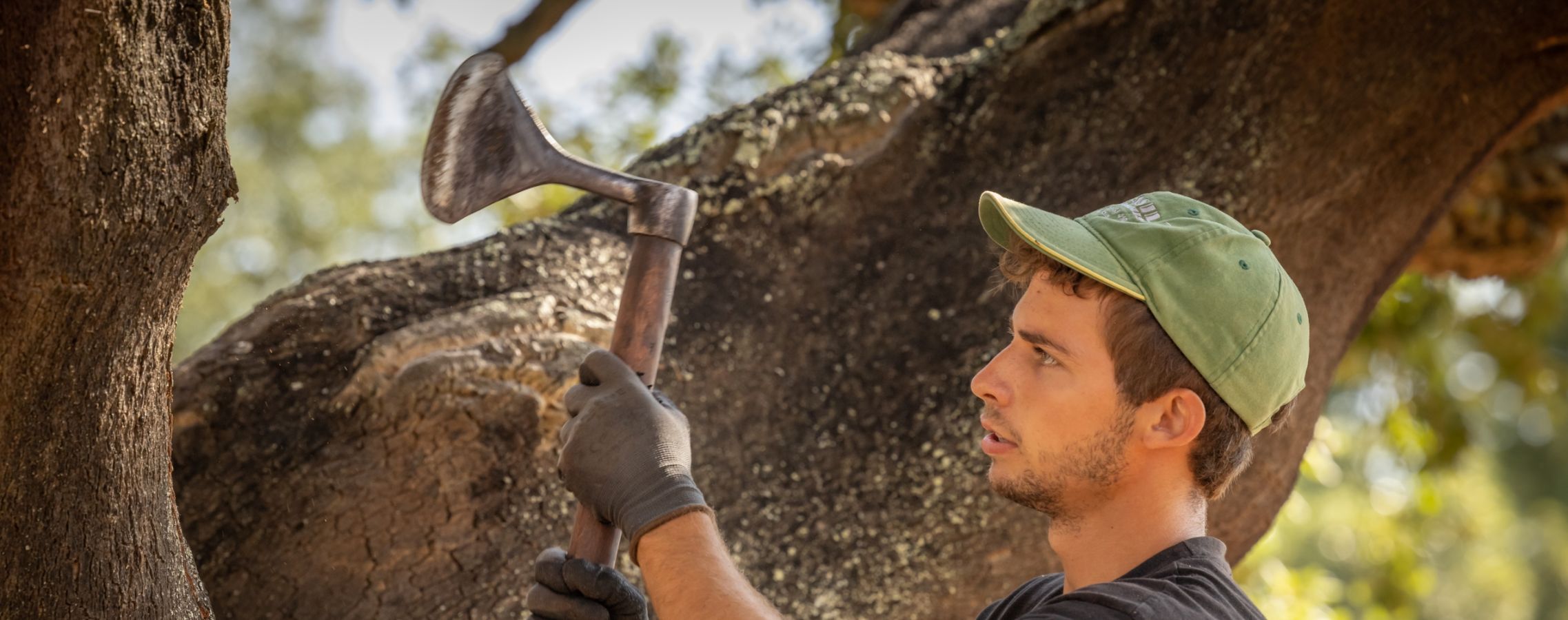
1. Opening

A horizontal cut defines the size of the cork plank to be removed and what is to remain on the tree. During dividing, the inner bark is frequently marked and these mutilations can sometimes alter the geometry of the trunk.

The plank is then separated from the tree, by inserting the edge of the axe between the strip and the inner bark. The axe is twisted between the trunk and the cork strip to be extracted.

The plank is then separated from the tree by inserting the axe's edge between the cork plant's belly and the bark. Then with a twisting movement of the axe between the trunk and the cork plank, the cork is removed. The larger the planks extracted are, the greater their commercial value. The removal of entire planks depends on the skill of the workers. After the first plank has been stripped, the operation is repeated over the whole trunk.

After the stripping of the planks, some fragments of cork remain attached at the base of the trunk. To remove any parasites in these "wedges", the descortiçador gives them a few taps with his axe.

Finally, the tree is marked, with the last number of the year in which it was harvested.
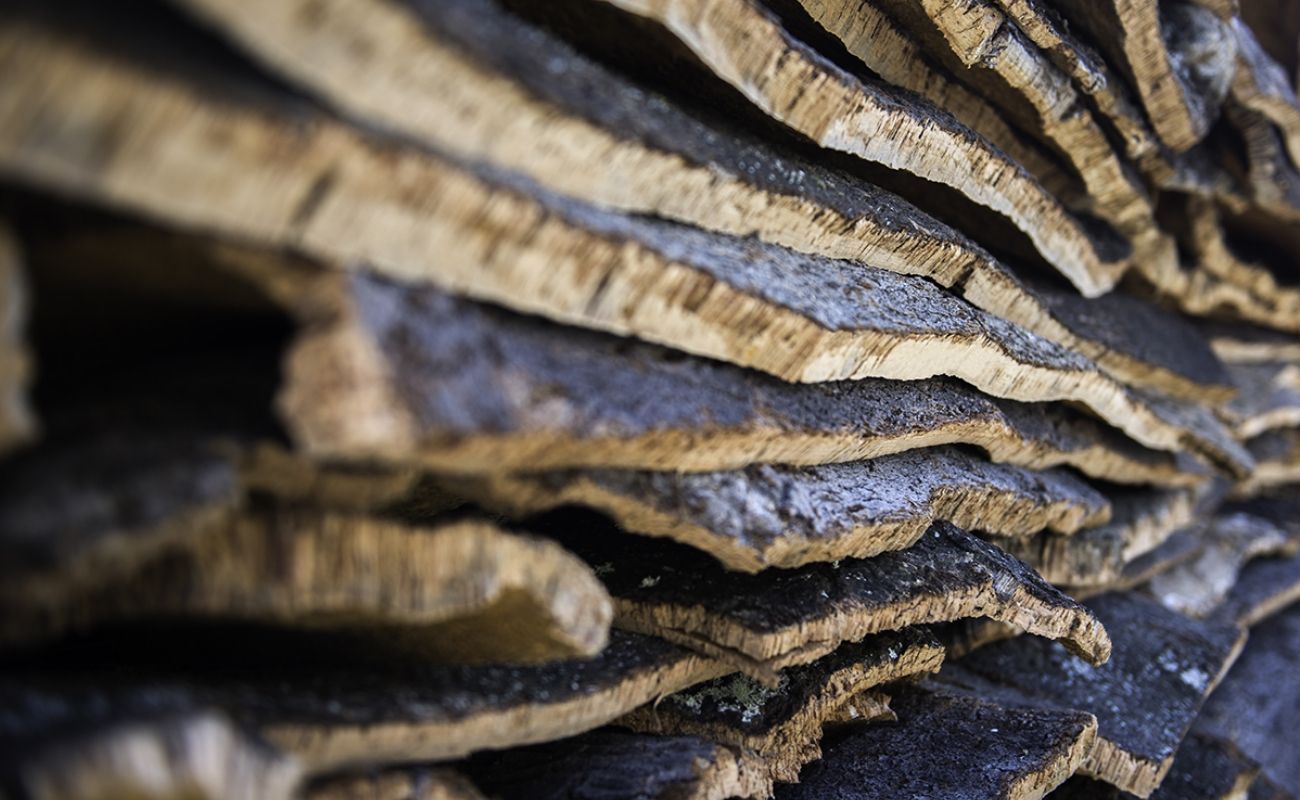
Rest period
- Clean the cork
- Extract water-soluble substances from it
- Increase its thickness and thus reduce its density
- Make it softer and more elastic

Stabilization
After cooking, the cork stabilizes. It is only after this period, which lasts two to three weeks, that the boards are sorted. Stabilization serves to flatten the planks and allow them to rest. This is the only way for the cork to obtain the consistency it needs to be transformed into stoppers.
Stabilization also allows the cork to reach the ideal moisture content for processing, which is around 14 percent.
The cork planks are then cut (rabbeted) into strips slightly wider than the length of the cork stopper to be made. Natural cork stoppers are punched from a single piece of cork, whereas technical stoppers are produced from a body consisting of agglomerated cork granules, to the ends of which natural cork discs may be applied.