Composite agglomerate, commonly known as "white agglomerate", is made by agglomerating cork granules which can also be mixed with other materials such as rubber, plastic, asphalt, cement, plaster, casein, resins and glues, giving rise to composite agglomerates, thus obtaining a wide variety of products.
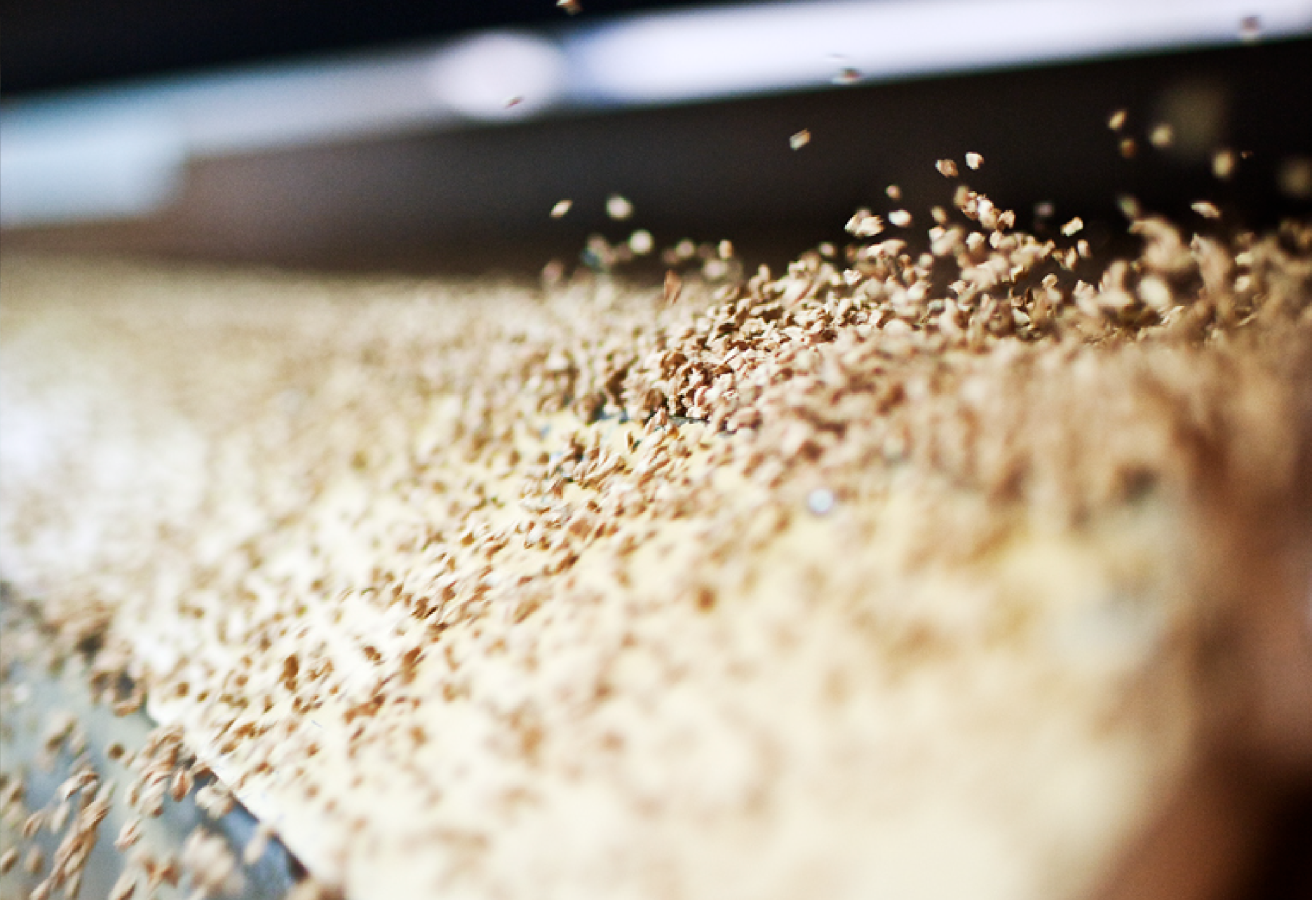
Granulation
The cork used to make construction and decoration materials comes from the first and second bark extracted from the cork oak tree, which is not used for stoppers, and from the scrap, shavings, bits and pieces of cork waste from other industrial units. The cork is grinded and comes in various grain sizes (usually more than 0.25 mm and less than 22.4 mm) and density (usually 70-90 kg/m3). The granules are obtained through the action of various types of mills, taking into account the material to be crushed and the type of granules required.
After grinding, it is usual to clean the granules, followed by drying by forced circulation of hot air, using rotary dryers, which give the granules the desired degree of humidity.
Agglomeration
These granules are the raw material for the production of agglomerates which are the result of a process of agglutination of granules with a specific particle size and density and the joint action of pressure, temperature and a binding agent, depending on the product and intended application.
After automatic or manual dosing, the granules are mixed with the binding and possibly other auxiliary agents using a mechanical process - paddle or helical mixers. The density of this process depends on its intended purpose. For example, agglomerates for decorative purposes use values of between 200 and 350 kg/m3 and fine-medium sized granules; for floor coverings the density is between 450 and 600 kg/m3; and for expansion joints (cork is used between rigid elements, namely concrete, as acoustic and thermal insulation) the size is medium and the density varies between 250 and 350 kg/m3. Synthetic polyurethane, phenolic and melamine resins or resins of plant origin are used for this agglutination.
During the agglomeration phase, the granules can also be colored with pigments, enabling different colors.
After automatic or manual dosing, the granules are mixed with the binding and possibly other auxiliary agents using a mechanical process - paddle or helical mixers. The density of this process depends on its intended purpose. For example, agglomerates for decorative purposes use values of between 200 and 350 kg/m3 and fine-medium sized granules; for floor coverings the density is between 450 and 600 kg/m3; and for expansion joints (cork is used between rigid elements, namely concrete, as acoustic and thermal insulation) the size is medium and the density varies between 250 and 350 kg/m3. Synthetic polyurethane, phenolic and melamine resins or resins of plant origin are used for this agglutination.
During the agglomeration phase, the granules can also be colored with pigments, enabling different colors.
Molding
The granules and resins are then placed in molds, usually metallic and in the shape of a parallelepiped – for cork rolls, cylindrical molds are used -, followed by a pressing. The molds are subsequently placed in an oven, which can be heating ovens (using temperatures ranging between 110 ºC and 150 ºC and for a period of 4 to 22 hours) or continuous high-frequency systems (tunnels) or discontinuous (the molds used are made of fiberglass and can be ready for handling in 3 - 4 minutes).
Then, demolding and cooling/ stabilization are carried out, obtaining a block capable of being laminated into sheets. There is another molding system called matting. In this case, the granules, binders and agents are mixed and placed on a conveyor belt and when passing through a heated plate press, at a temperature of 120 - 180 ºC, they are agglutinated together forming a single sheet of the desired thickness.
The next phase is sanding, which allows the thickness and degree of roughness of the cork sheet to be adjusted. The sheets are then cut into a rectangular or square shape, adjusting after the dimensions and squareness.
Then, demolding and cooling/ stabilization are carried out, obtaining a block capable of being laminated into sheets. There is another molding system called matting. In this case, the granules, binders and agents are mixed and placed on a conveyor belt and when passing through a heated plate press, at a temperature of 120 - 180 ºC, they are agglutinated together forming a single sheet of the desired thickness.
The next phase is sanding, which allows the thickness and degree of roughness of the cork sheet to be adjusted. The sheets are then cut into a rectangular or square shape, adjusting after the dimensions and squareness.
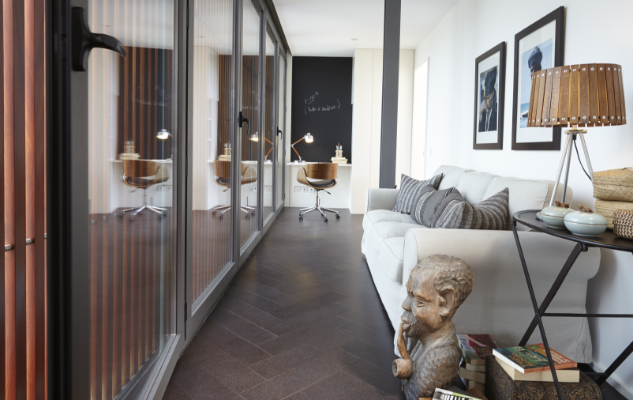
Visual
Once the sheets have been obtained, the various types of decoration and coverings need to be made. These can be done either with a single sheet or by overlapping several sheets of agglomerated or laminated natural cork, or by composing them with other materials - wood or others. The various sheets are glued together using rollers or a specific type of press. The boards are formed and can have various types of surface finish: varnish, wax, paint or covered with particles such as PVC. Some companies also offer the possibility of printing a design, photograph or pattern on cork (Digital Printing)...The limit is our imagination!